お知らせ
事例5 調理設備導入に伴う生産性向上による製造コスト低減
本事例は「食品原材料調達安定化対策事業(農林水産省)」によるものです。
同事業のその他の事例はこちらの一覧から閲覧できます。
株式会社エス・デリカファクトリー(千葉県)
事業:弁当・惣菜類の製造・販売
従業員:82名
価格高騰の影響を受けていることが証明されている輸入原材料:鶏肉・豚肉
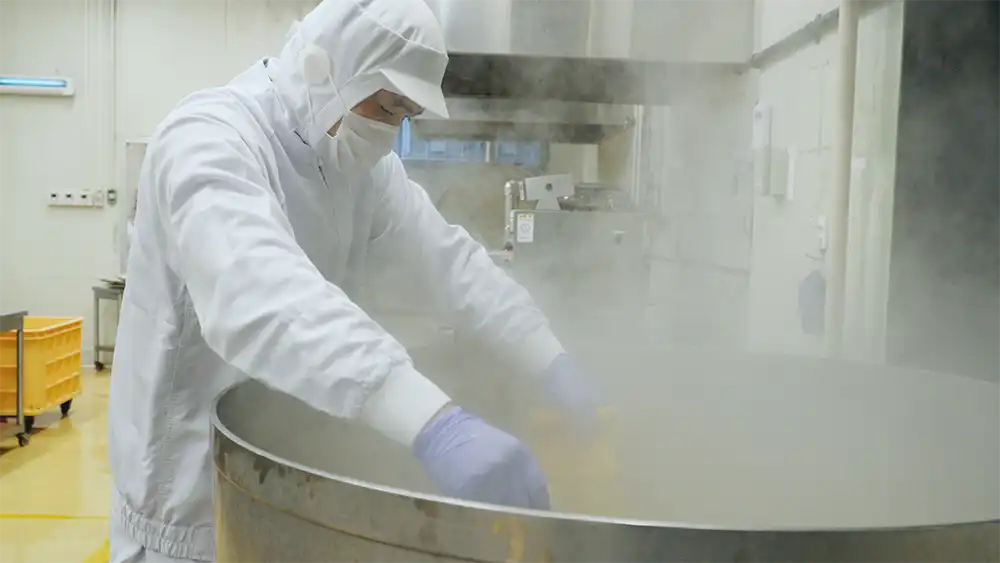
輸入食材の価格高騰を機に、新たな設備投資を決意
千葉県に工場を持ち、主に東京を商圏として弁当や惣菜の製造・販売事業を展開する株式会社エス・デリカファクトリー。都内40か所のオフィスビルに昼食用弁当を提供するほか、スーパーマーケット向けの惣菜原料供給も手掛けています。弁当のラインナップは約20種類。味、ボリューム、そしてエスニックメニューなども取り入れた商品バリエーションも同社の特徴で、毎日9,000パック以上を製造・販売しています。
もともとエス・デリカファクトリーは弁当の製造・販売を中心に事業を展開していました。しかし、コロナ禍の影響により業績が大きく低下したことで、新たに惣菜事業をスタート。この取り組みが奏功し、2021年度はわずかながらも単年度黒字となりました。
その後も同社は弁当と惣菜の両輪で順調に業績を伸ばし続けますが、その一方で、新たな問題が発生します。ウクライナ紛争や円安によって、サバや鶏肉、豚肉といった原材料の仕入れ価格が高騰し、収益を圧迫し始めたのです。
エス・デリカファクトリーでは、このような状況を受けて、一度、商品の値上げを試みました。しかし、その効果は限定的であり、また、再度の値上げも難しいことから、収益性改善には原価の圧縮が必要だと考え、さらなる原材料費と人件費の削減に取り組むこととなりました。
原材料費の削減に関しては、海外の生産地に出向いて供給元と直接価格交渉する、国内メーカーと直接交渉し、ロットをまとめて調達する、といった方法で費用を圧縮。人件費の削減に関しては、中食ニーズの高まりから惣菜マーケットは今後も拡大が見込めるとの推測に基づき、「原材料費上昇への対策」だけでなく「新たなビジネスチャンスへの積極参入」も考慮すべきと判断。そのためには、生産ラインの抜本的な改善が必要であると考え、新たな設備投資を決断しました。
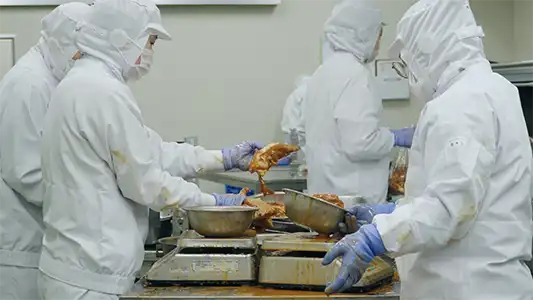
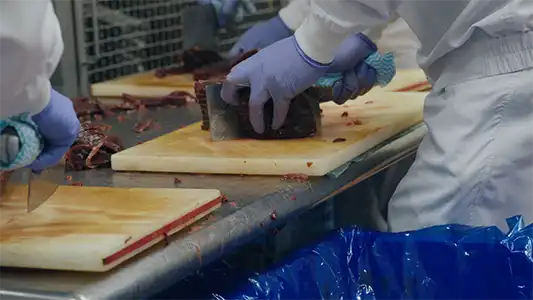
過去の経験と関係各所の知見をもとに生産ライン全体を最適化
従来の設備では手作業に頼らざるを得ない部分が相当にあったため、生産ラインの再整備は、手作業の工程を自動化することで生産性を上げるという方向で進められました。
生産ラインのコストと能力を最適化するには、特定の工程の強化だけでは不十分。生産ライン全体を見渡しつつ、工程ごとに改善の幅と費用対効果を見極め、それに基づいて最適な機材を過不足なくバランスよく配置する必要があります。エス・デリカファクトリーでは、機器メーカーや販売代理店などから専門的な知見を得て、機器の選定や導入プランを検討。その結果、本事業を活用して4種類の機器を各1台導入しました。
大量の食材を総じて計量できる「大型計量器」。増設により2倍の食材を攪拌できる「トローリータンブラー」。食材の充填、包装、印字までを自動で行う「充填包装機」。増設によりボイル量が増大した「回転釜」。これらの機器を導入したことで生産性が向上し、人件費は従来の70%に抑えられ、生産コスト全体では8.6%の削減効果を実現しました。
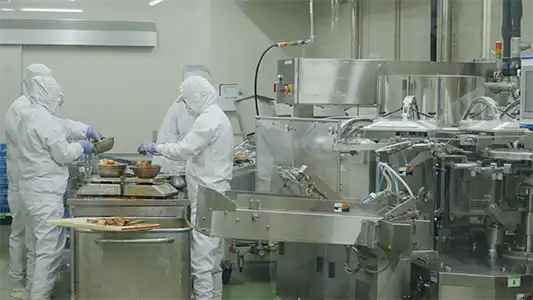
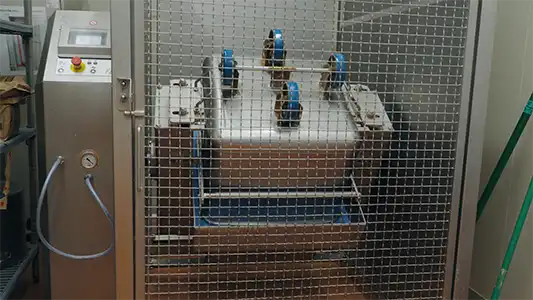
また、手作業の工程を自動化したことで、人的ミスに起因する原材料ロスの削減、仕上がりの均一化、商品衛生レベルの向上、機器の洗浄時間や、それに使用する水資源の削減という副次的効果も生まれています。
エス・デリカファクトリーでは、新たな機器が導入された生産ラインで、従来商品の刷新にも着手。従来の調理法にひと手間加えることで、豚の角煮や鶏の唐揚げなどを、よりカロリーの少ないヘルシー版にアップデートしました。調理の工数は増えるものの、機器導入によって生産コストが下がった分を充当することで、値上げすることなく、より付加価値の高い商品をお客様に提供しています。
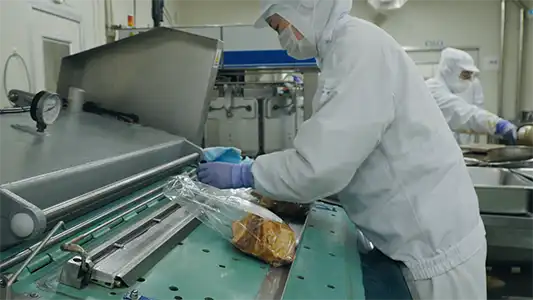
本事業実施による成果
【設備導入による原料価格(3か月間)の低減】
事業実施前50.5百万 → 事業実施後46.2百万
【生産性向上による製造コスト(3か月間)低減】
惣菜:事業実施前138円/kg → 事業実施後134円/kg
弁当:事業実施前183円/kg → 事業実施後178円/kg
中食ニーズの増加をビジネスチャンスと捉え、さらなる事業拡大へ
エス・デリカファクトリーでは、中食ニーズの増加を背景に事業のさらなる拡大も目指しています。日本には大手チェーン以外にも中小規模のスーパーマーケットが数多くありますが、その中には十分なサプライチェーンを確立できていない事業者も少なくありません。今後は、そういったところにアプローチすることでビジネスチャンスを広げたいとしています。
また将来的には、スーパーマーケットの店頭やインターネット宅配などで一般消費者に直接販売するB to C事業も構想しており、そのための打ち手として、今回導入した機材を用いたさらなる生産性向上、オリジナル商品の開発、第2工場の設置などに取り組む予定です。
本事業のポイント
ボトルネックの把握・設備導入効果の最適化には「製造工程の全体把握」が重要
本事業では、計量器や調理窯等の導入により、原料価格や製造コストの削減を実現しました。大幅なコスト削減のためにはライン全体の生産性向上、つまり複数設備を導入する必要があります。こちらの事業者では、各製造工程の効率把握をしており、それにより「どこに設備を導入することで製造効率を最適化出来るか」を事前に検討できたことが大きな成功要因と言えます。目に見えるボトルネックはもちろん、潜在的なボトルネックが生産性に影響している可能性も大いにあります。特定工程にだけ着目するのではなく、全ての製造工程の現状を把握することが、適切な設備導入及び一連の製造工程の最適化に大きく意味を持つと考えられます。